Recently, the Falling Film Crystallizer, independently developed by DODGEN, was officially listed in the Catalogue of Advanced Processes, Technologies, and Equipment for Petrochemical Industry Transformation and Upgrade issued by the China Petroleum and Chemical Industry Federation. This recognition marks a significant milestone—DODGEN’s crystallizer has received authoritative national acknowledgment for its role in high-end chemical material manufacturing.
Currently, the DODGEN Falling Film Crystallizer has achieved industrial application in the purification of electronic-grade ethylene carbonate (EC), commanding 56% of the domestic market share.
In the following section, we will dive deep into electronic-grade carbonates and the low-carbon separation technologies behind them.
【About Carbonates】
Classification of Carbonates
Carbonates are mainly classified into cyclic carbonates and linear carbonates.
Cyclic carbonates include ethylene carbonate (EC), propylene carbonate (PC), vinylene carbonate (VC), and fluoroethylene carbonate (FEC).
Linear carbonates include dimethyl carbonate (DMC), diethyl carbonate (DEC), and ethyl methyl carbonate (EMC).
Main Process Route
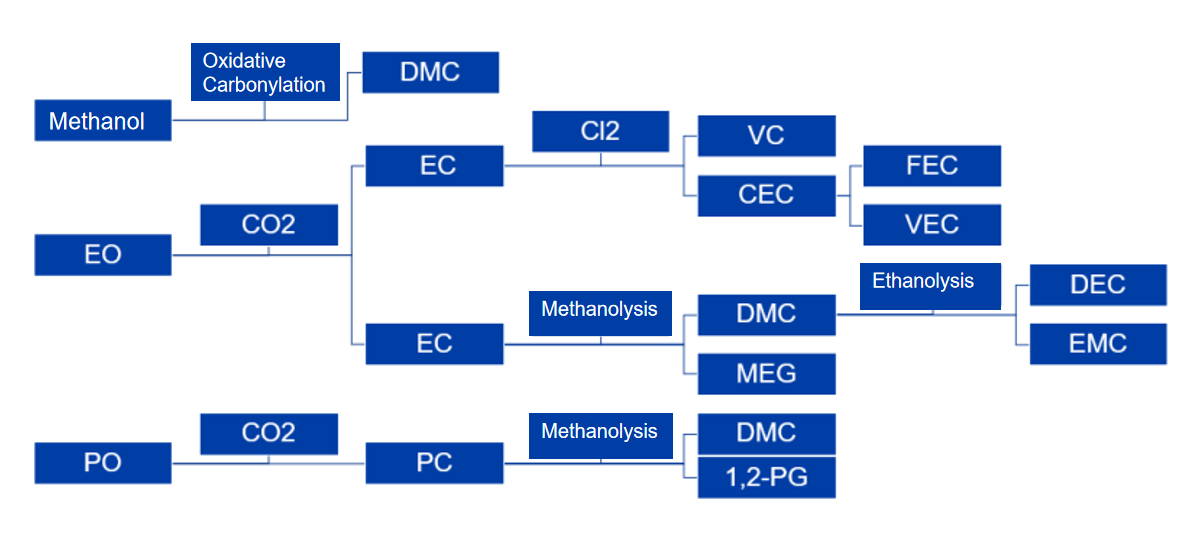
Electronic-grade carbonates, as high-purity and high-performance chemical materials, are widely used in high-tech fields such as new energy, electronics, and automotive industries. As core solvents and additives in lithium-ion and sodium-ion battery electrolytes, they play a crucial role in determining the battery’s conductivity, cycle life, safety, and overall production cost.
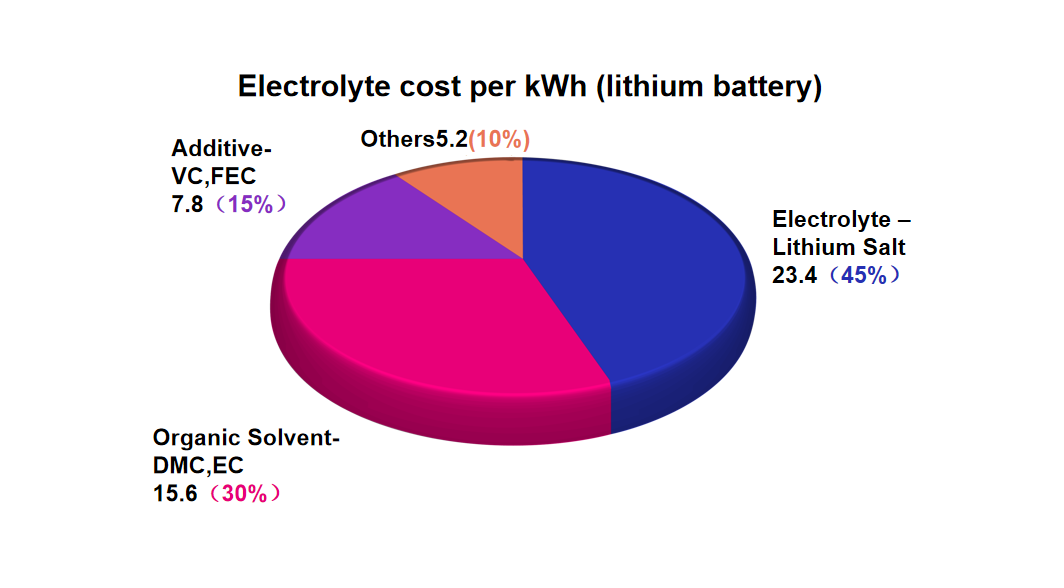
【Industry Standards——DODGEN Collaborates on Standard Development to Promote Industry Regulation】
In recent years, driven by the rapid growth of new energy vehicles and energy storage, China's electrolyte industry has developed at an impressive pace. However, the construction of a mature industry standard system still lags behind, leading to varying quality levels of electronic-grade carbonates.To address this, DODGEN has collaborated with leading industry players to co-develop two key group standards: “Evaluation Requirements for Green Factories Producing Lithium Battery Electrolytes” and “Carbon Footprint Guidelines for Lithium Battery Products: Electrolyte.”
The following table summarizes the commonly adopted specification requirements for electronic-grade carbonate products in the current market:
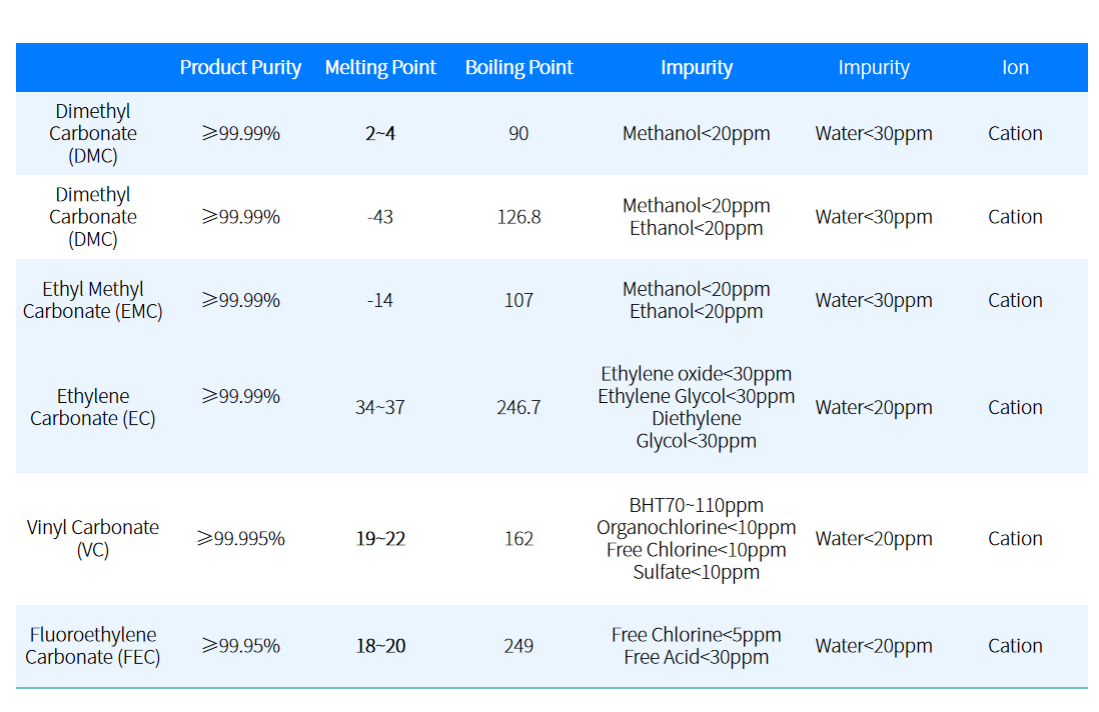
【Low-Carbon Separation Technology——DODGEN’s Melt Crystallization: Enhancing Purity, Reducing Energy Consumption】
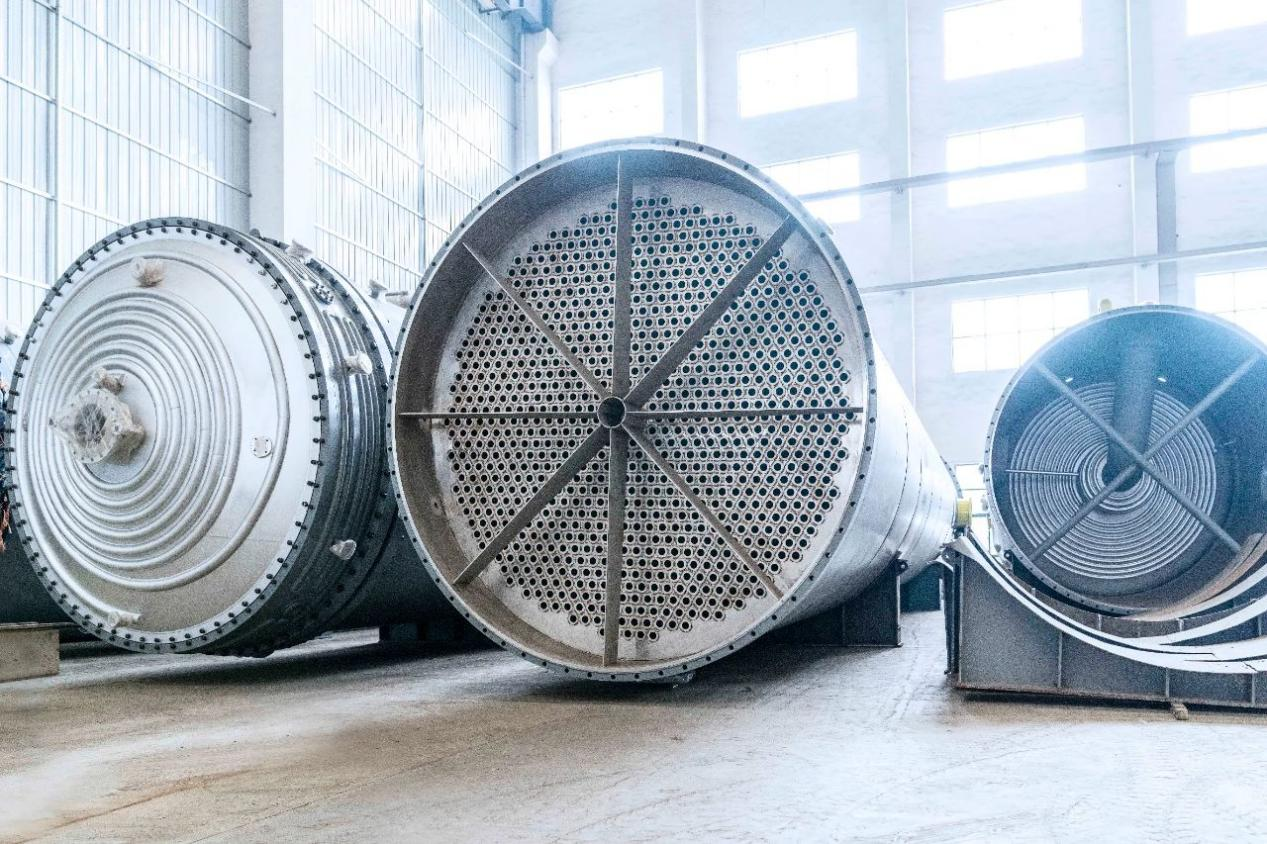
Driven by the rapid growth of new energy vehicle sales and energy storage demand, the global demand for electrolyte products is surging. In 2022, China shipped 891,000 tons of electrolytes, accounting for 85.4% of global output. Global demand is projected to reach 2.62 million tons by 2025 and exceed 8 million tons by 2030. However, China’s electrolyte production capacity already reached 4.29 million tons in 2023, with a capacity utilization rate of less than 40%, indicating significant overcapacity that will be difficult to digest in the short term.To remain competitive, the industry must break through via technological upgrades, cost optimization, and global expansion.
DODGEN’s low-carbon separation technology enables both energy savings and quality enhancement in electronic-grade carbonates, significantly boosting the industry's competitiveness.
Challenges of Traditional Separation Technologies
The traditional separation method for electronic-grade carbonates is distillation, but there are several challenges in the distillation process for electronic-grade carbonates:
Azeotropes: For example, Dimethyl Carbonate (DMC) forms an azeotrope with methanol. The current mainstream method to avoid the azeotrope point is pressure-swing distillation. However, this process has drawbacks such as multiple distillation columns, high energy consumption, numerous impurities in the products, and unstable product quality.
Close boiling points: For instance, the boiling point difference between Vinyl Carbonate (VC) and its impurity, diethylene glycol, is only about 2°C at normal pressure, which leads to significantly increased separation energy consumption.
Thermal sensitivity: Carbonates typically have thermal sensitivity, meaning they tend to decompose or polymerize at high temperatures. For example, the thermal sensitivity temperature of Vinyl Carbonate (VC) is around 60°C, and high-temperature separation negatively impacts the product yield.
High purity requirements: With the exception of Fluorinated Ethylene Carbonate (FEC), other electronic-grade products require purity levels of 99.99% or higher. Since the separation factor of distillation decreases as product purity increases, the energy consumption for separating high-purity products increases exponentially.
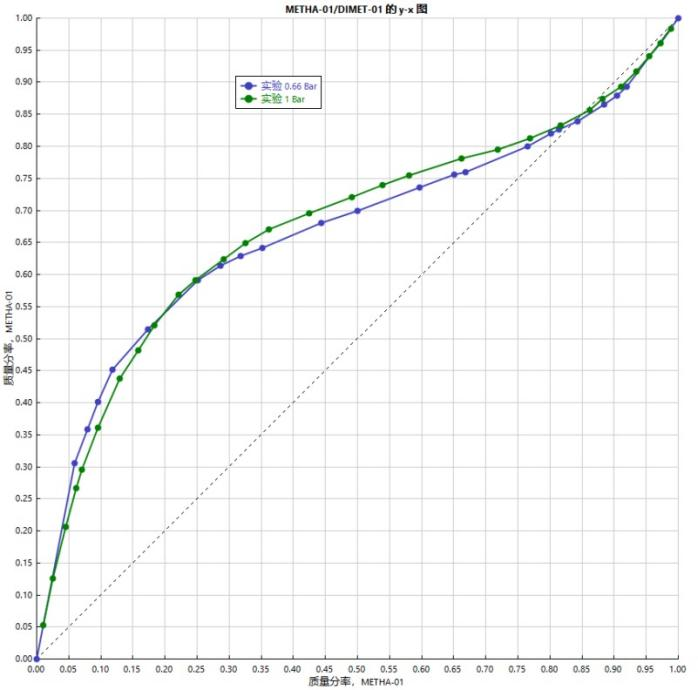
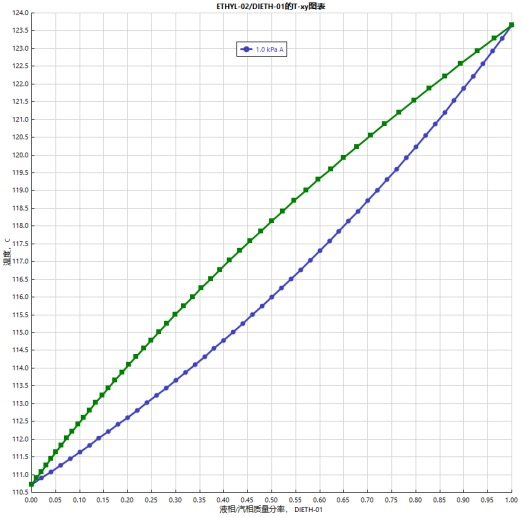
To address the separation challenges of electronic-grade carbonates, DODGEN has adopted "Melt Crystallization Technology" and the "Melt Crystallization-Distillation Coupling Process" to replace traditional separation technologies. This approach has not only improved product quality but also significantly reduced production energy consumption, opening up a new pathway for the purification of electronic-grade carbonates.
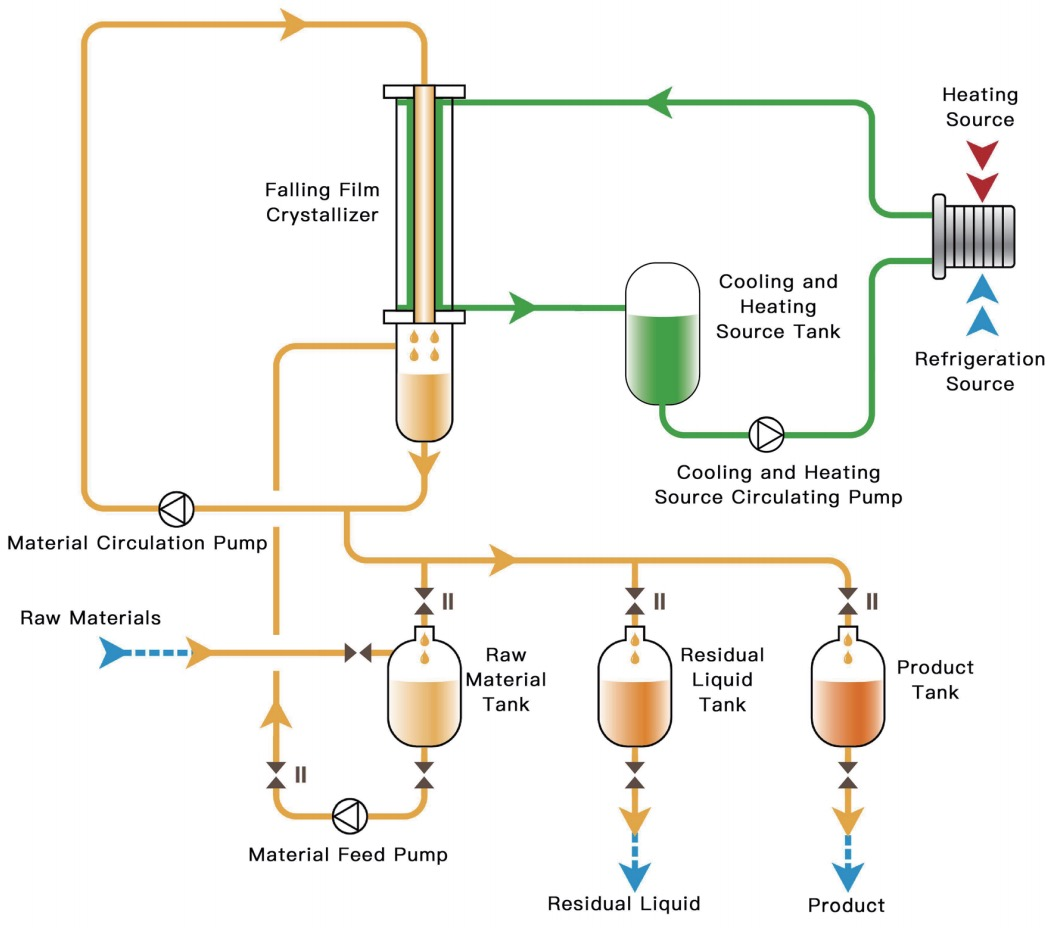
Unlike traditional distillation, which separates components based on the boiling point differences between the main substance and impurities, melt crystallization separates components based on differences in melting points. The driving force of the process is the supersaturation or undercooling of a component in the molten liquid. The process consists of two main steps: crystallization and sweating.
In the crystallization process, as the temperature of the molten liquid gradually decreases, a component reaches supersaturation and begins nucleating, growing into crystals. During this crystal growth process, impurities from the mother liquor are inevitably trapped or adhered to the rough crystals. Therefore, after crystallization, a sweating process is required to further purify the product and obtain a high-purity product. Typically, electronic-grade carbonates require a multi-stage segmented process to achieve high purity.
Advantages of DODGEN's Melt Crystallization Separation Technology
Compared to traditional distillation, melt crystallization technology offers five core advantages:
Energy Efficiency:The latent heat of melt crystallization is typically only 1/7 to 1/3 of the vaporization heat in distillation. When considering the high reflux ratios and heat losses in distillation, melt crystallization's energy consumption is only 10% to 30% of that of distillation.
Low-Temperature Operation:The crystallization process is generally performed at low temperatures and under normal pressure, which eliminates issues such as material volatilization and pollution. The process is simpler, safer, and requires less stringent equipment material requirements due to the reduced corrosiveness at lower temperatures, lowering both operating costs and fixed investments.
Ultra-High Purity:Melt crystallization can separate higher purity products. The separation factor in melt crystallization can be very high and is not affected by product purity. With experience, product purity levels of 99.999% and above have been achieved.
No Solvent Introduction:For isomers and heat-sensitive materials, distillation often requires many distillation plates, high reflux ratios, and vacuum operations. These harsh conditions, along with high demands on equipment materials and precision, often lead to issues such as carbonization, coking, and polymerization in the distillation column, resulting in low product yield and inability to achieve high purity. Melt crystallization avoids these problems. For such systems, the melting points of substances often differ by dozens of degrees, making melt crystallization a viable separation technique. This method also avoids solvent contamination of products and reduces the need for solvent recovery.
Suitable for Special Materials:For isomers and heat-sensitive substances, distillation can be difficult and inefficient due to boiling point and thermal sensitivity issues. Distillation requires numerous distillation plates, high reflux ratios, and vacuum operations, leading to high operational complexity and stringent equipment requirements. Even with such efforts, issues like carbonization and polymerization remain unavoidable, lowering yield and purity. Melt crystallization, on the other hand, can address these issues effectively, especially for systems where substances’ melting points differ significantly.
DODGEN Case Study
As of now, DODGEN has implemented dozens of industrial-scale melt crystallization cases in the electronic-grade carbonate field. Below, we compare traditional separation processes with melt crystallization separation technology using Ethylene Carbonate (EC) as an example.

The production process of Ethylene Carbonate (EC) involves the reaction of Ethylene Oxide (EO) and Carbon Dioxide (CO₂) in the presence of a catalyst inside a reactor to generate EC. After the reaction, the catalyst is recovered through flash evaporation. The mixture then enters the light-component removal column to obtain industrial-grade EC, which is further refined in a purification column to produce electronic-grade EC. The steam consumption in the separation section typically ranges from 1.2 to 1.8 tons of steam per ton of product.
Traditional Process Flow:
Reaction → Flash Evaporation → Light-Component Removal Column → Purification Column
Main Drawbacks of the Traditional Process:
High Steam Consumption in the separation section
Large Fluctuations in Product Purity
Extensive Space Requirement
DODGEN provided a customized retrofit solution for the client’s separation system by completely replacing the traditional distillation units (light-component removal column and purification column) with a melt crystallization system.
Results After the Retrofit:
Steam consumption reduced by 70%,from 1.3 tons of steam per ton of product to approximately 0.3 tons per ton
Product purity increased significantly, reaching 99.998%
Impurity removal efficiency greatly improved
Plant footprint reduced by 30%
Annual economic benefit of nearly 10 million RMB saved
Detailed energy consumption indicators are shown in the table below:
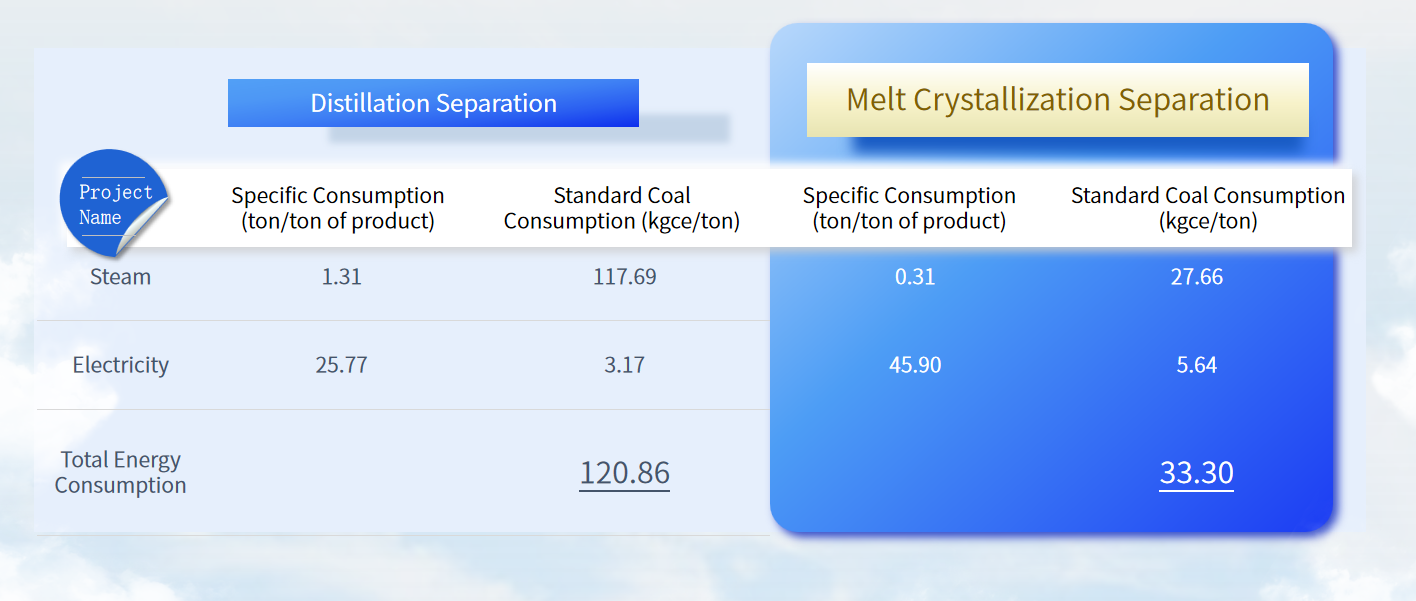